+++ Dingolfing Plant 02.10 takes electrically heated hardening furnace into series operation +++ Site uses innovative power-to-heat technology for the first time +++ Furnace saves some 300 tonnes CO2 a year +++
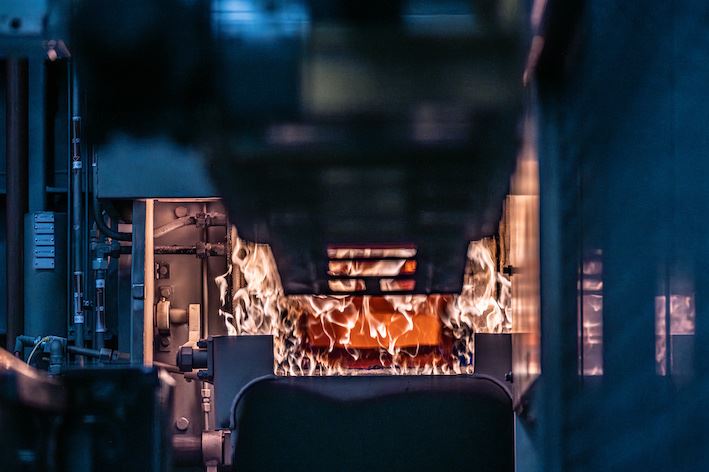
For the first time, chassis and drive component production in Plant 02.10 at the BMW Group site in Dingolfing is operating an electrically heated ring hearth furnace. Compared with its conventional gas-powered equivalent, the latest electric furnace currently saves some 300 tonnes of CO2 a year.
“The new furnace has a planned service life of over 40 years, so it’s a future-focused piece of equipment that sets the course for our journey to net zero,” said Marc Sielemann, responsible for quality and production of powertrains, chassis and brakes with Purchasing, and director of the Dingolfing component plant 02.10. The BMW Group has set itself the target of being climate neutral along the entire value chain by 2050 at the latest.
With its innovative power-to-heat technology, the hardening furnace came at an investment of approx. €7 million.
New hardening furnace for e-drive components
Plant 02.10 in Dingolfing produces chassis and drive components for BMW, MINI and Rolls-Royce vehicles. To make them more hard-wearing, the parts are hardened in special furnaces. As electric mobility ramps up, more and more components are being manufactured, including for electric drives. Existing systems are gradually reaching the limits of their capacity, so a new ring hearth furnace with a fixture hardening press was needed.
Used to harden gear wheels for electric transmissions, the innovative system has production capacity of approx. 960,000 spur gears a year. What’s special about it is that unlike the two existing furnaces, which are powered by gas, a fossil fuel, this new solution is for the first time powered by electricity. Rather than using 33 gas flames in ceramic-jacketed pipes, as the older model does, the new furnace uses the same number of electric heating elements to heat up to 900 degrees Celsius.
Lower CO2 emissions
Electric heat generation – or power-to-heat technology, as it is called – saves vast amounts of greenhouse gases, which are harmful to the climate. By running on electricity, the new hardening oven emits approx. 300 tonnes less CO2 a year than its gas-powered equivalent.
“Energy-intensive power-to-heat systems like this new electric ring hearth furnace support the decarbonisation of heat generation – an essential aspect of climate protection. They generate heat by climate-friendly means and can be powered among other things with excess energy from renewables,” said Sielemann. So, the new power-to-heat furnace not only reduces gas consumption at Plant Dingolfing but also supports the integration of renewable energies into the electricity grid. It is another component in BMW Group Plant Dingolfing’s transformation to a sustainable BMW iFACTORY. “For the future,” said Sielemann, “we are looking into converting the remaining hardening furnaces to electricity as well.”
BMW PRESS